Bent Concrete Side Table
FOUR: CASTING CONCRETE
As the saying goes “timing is everything”. To successfully cast this table you need to bend the concrete when it’s at the optimal “plastic” state. If you attempt to bend the concrete too early it’ll slump down the form into a pile of mess and if you wait too long it’ll crack at the curved points.
Step 1 – Prepare Casting Table
Step 2 – Mix Activator and Pigment
Step 3 – Add Fiber-Reinforced Concrete Mix
Step 4 – Consistency for Casting
Step 5 – Pour Concrete
Step 6 – Bend
Step 7 – Bend and Cure
Previous: Cast Rubber Mold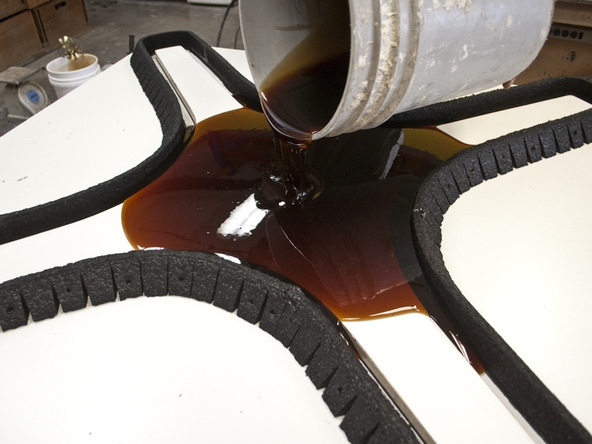
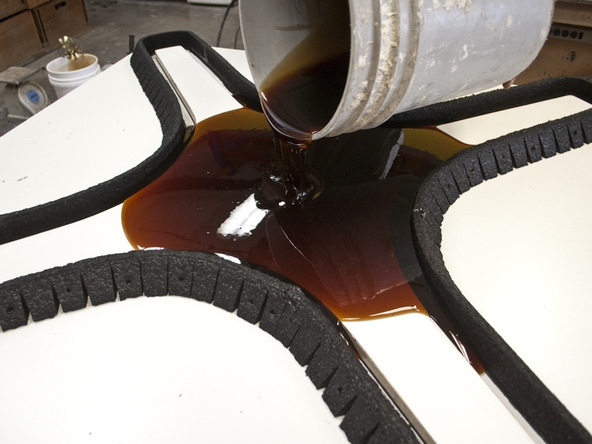
Polyurethane mold rubber behaves like glue and will stick to most materials, so make sure that all surfaces are protected with Pol-Ease Mold Release.
Next: Demolding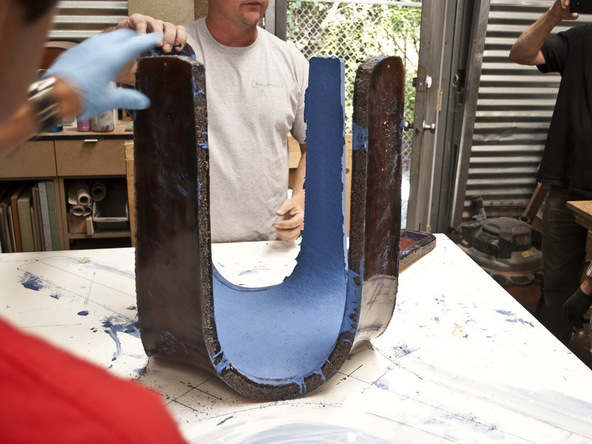
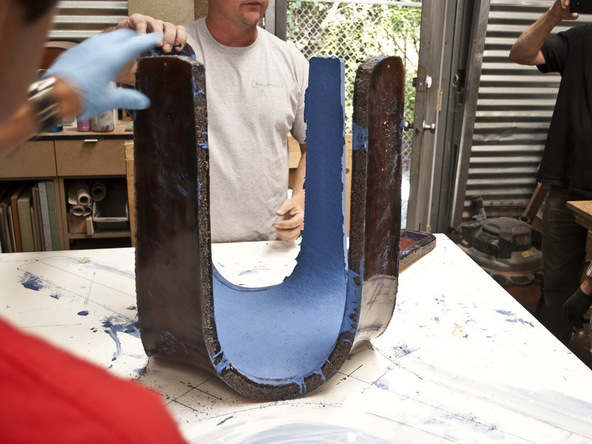
Wait 24 hours before attempting to demold this project. The legs will continue to be delicate until the concrete has reached full strength in seven days.