Fabric Formed Concrete Fire Table
ONE: FORMING
The formwork does not need to be exceptionally strong because this is a hollow, fiber-reinforced piece. The form is constructed from 3/4″ Melamine that’s been ripped to size on a table saw.
What You’ll Need
- Heavy Duty Stapler
- Staples
- Table Saw
- Cordless Drill
- 1-1/4″ Drywall Screws
- Pre-Drill and Countersink Bit
- Stinson Fire Table Instructional Drawings
- 19″ Burner Assembly
What You’ll Need
- Control Box
- Vinyl Upholstery Fabric
- 1″ Insulating Foam
- 2″ Insulating Foam
- 1/8″ Luan
- Foam-Lok Adhesive
- Clear Packing Tape
- Contact Adhesive
Step 1 – Burner Knockout
Step 2 – Control Box Knockout
Step 3 – Burner Knockout 2
Step 4 – Fabric Form
Step 5 – Fabric Form
Step 6 – Form Walls
Step 7 – Install Feet and Control Box Knockout
Next: Vacuum Hookup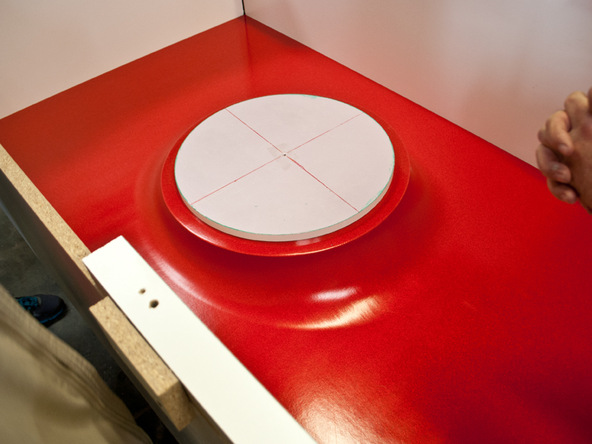
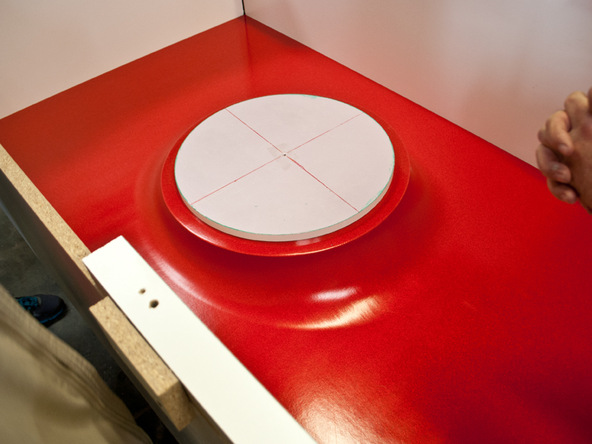
A shop vac is attached to the form base during casting to provide suction that pulls the vinyl fabric into graceful curves around the rigid foam risers.