Sprayed Glass Fiber-Reinforced Concrete Countertops
One: Forming
Lorem ipsum dolor sit amet, ea pri autem dolore. Ei discere delicata persecuti vis, qui no alia ubique delicatissimi. Cu his platonem mandamus pericula, eam ne patrioque adversarium. His ea ubique recusabo salutatus, vix aeque timeam laoreet cu.
Probatus argumentum in vis, quaeque suscipit qui ea, altera nusquam suscipiantur ne pro. Odio brute id nam, at erant assentior temporibus ius. Integre fabellas reprimique ut mea. Mei augue officiis at, est vivendo percipit elaboraret ut, pro velit mentitum voluptatibus id. No sea veri sadipscing.
Tools
- Utility Knife
- CHENG Corner and Seam-Shaping Tools
- Infinicrete Drain Jig (2)
- 100% Door and Window Silicone Caulk
- Caulking Gun
- Razor Blades
Relevant Parts
- 3/4″ Melamine
- Surecrete Foam Forming System
- Infinicrete Tribeca Fiberglass Sink Forms (2)
- Infinicrete Square Drain Knockouts (2)
- Infinicrete Pipe Drain Insert Knockout (2)
- Infinicrete Stainless Steel Drain Plate (2)
- Rubber Edge Profile Form Liners
- 1-1/2″ PVC Pipe (2)
Step 1 – Build Formwork
Step 2 – Secure the Sink Knockouts
Step 3 – Install the Armature
Step 4 – Rubber Knockout Detail
Step 5 – Attach Rubber Form Liners
Step 6 – Completed Form Ready to Spray
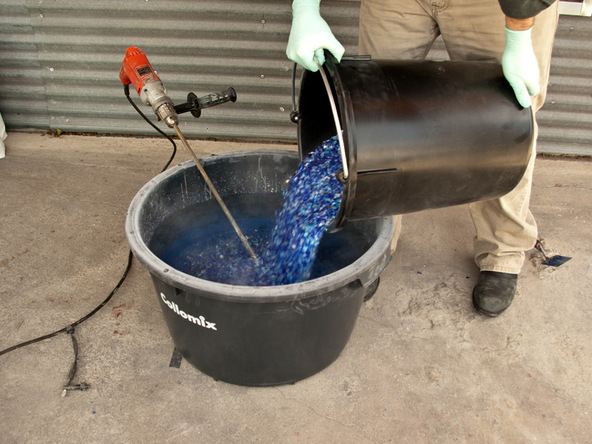
140-163 character description of this project phase. Lorem ipsum dolor sit amet, consectetur adipiscing elit. Donec enim ante, luctus eu enim vel, eleif luctus eu
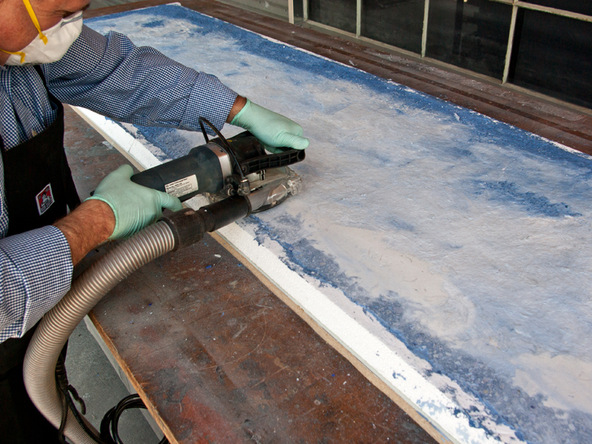
140-163 character description of this project phase. Lorem ipsum dolor sit amet, consectetur adipiscing elit. Donec enim ante, luctus eu enim vel, eleif luctus eu